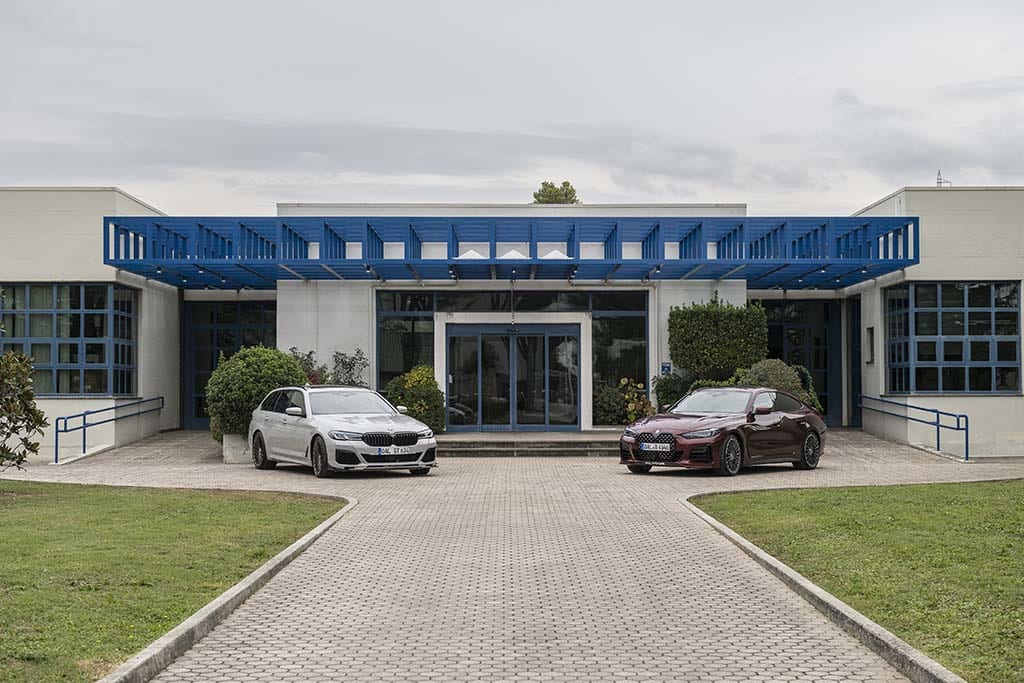
高級マテリアルとして高い評価を得ている「アルカンターラ」。今回はその工場を特別に見学する機会に恵まれた。“メイド・イン・イタリー”にこだわるアルカンターラ製造現場の最前線からリポートする。
アルカンターラ製造の最前線、そのすべてに迫る
自動車好きなら一度は聞いたことがある「アルカンターラ」という名前。プレミアムカーのシートやダッシュボード、ステアリングなどに使用される高級マテリアルであるアルカンターラは、そのすべてがイタリアにて製造されている。今回特別に、その工場を見学する機会に恵まれ、イタリアが世界に誇る高級マテリアルがなぜそうたりえたのか、その秘密に迫りたい。
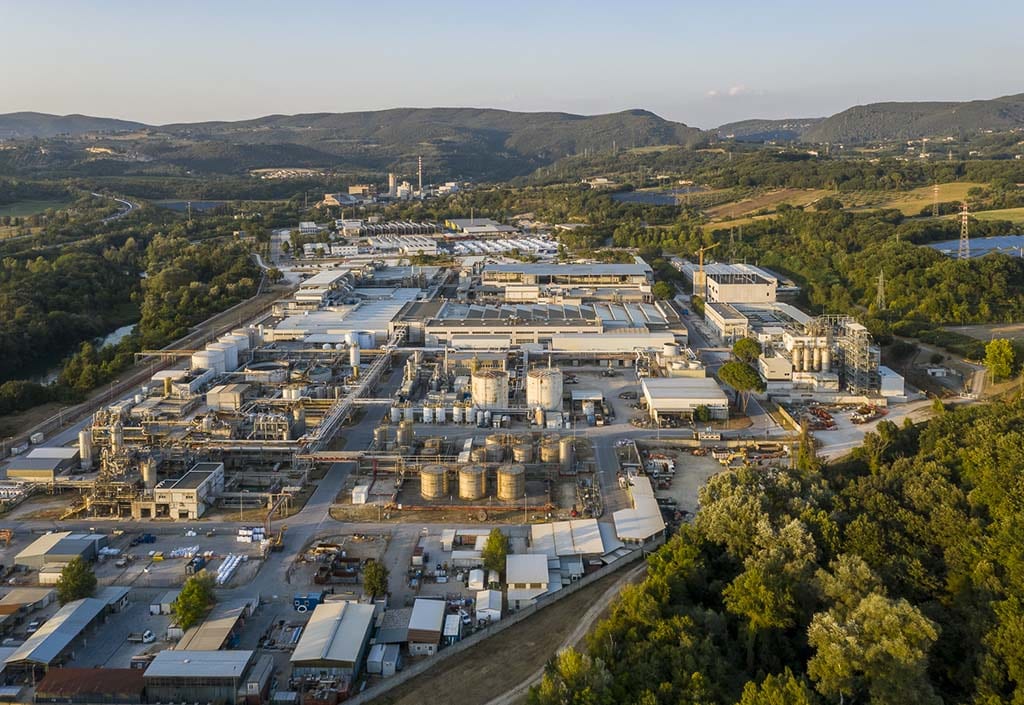
工場はローマからクルマで約1時間、ウンブリア州ネラ・モントロに位置する。全世界に出荷されるアルカンターラはすべてこの工場で生産されている。’19年には大幅な投資を行ない設備を拡張、生産能力をそれまでの2倍に引き上げた。
アルカンターラは1972年に「東レ」とイタリアの工業会社「Eni」の合弁によって設立された。東レが当時開発していた「エクセーヌ」という人工スエードを、アメリカでは「ウルトラスエード」という名で展開していたが、それのヨーロッパ版がアルカンターラというわけだ。つまり、アルカンターラのルーツは日本にある。とはいえその後の進化は、異なる道を歩むこととなる。
1988年、ランチア・テーマの内装にアルカンターラが初めて用いられたのを皮切りに、自動車分野への進出を開始。人工皮革でありながら、高い耐久・耐光性と、通気性や風合いと言った質感を両立するアルカンターラは、自動車の内装に最適で、瞬く間に高級マテリアルのひとつとして定着するに至った。
しかし、アルカンターラがここまで評価された理由はそれだけではなく、アルカンターラならではの〝おもてなし〟の流儀がある。
それがカスタマーのニーズに応えるテーラーメイドシステム「コンプレックス・マニュファクチュアリング」である。このシステムは染色やレーザーカット、ステッチといった2次加工において、カスタマーの要望に合わせた加飾を施すもので、同社が近年最も力を入れている分野だ。詳しい工法や加工については、次ページに譲るとして、アルカンターラはこれらの企画・加工・検品など、すべてを自社で研究・開発している。これらの工程をワンストップで行なうことで、製品として高いクオリティを維持できるだけでなく、余分なコストを抑えることもでき、アルカンターラの大きな強みにつながっているのだ。
今回訪れた工場には、これまで実際にコンプレックス・マニュファクチュアリングを用いて自動車向けに作成された商品の実物が展示されていたが、マセラティ、アルファ・ロメオ、フィアットといった「地元」企業をはじめ、ポルシェ、BMW、ルノー、フォード、トヨタ、日産……など各国の自動車メーカーが軒を連ねていた。これはひとえにアルカンターラの持つ高い技術力の賜物だろう。
サステナビリティの分野でも業界をリード
アルカンターラがもうひとつ、力を入れて取り組んでいるのはサステナビリティの分野だ。
2009年、同社はイタリアの工業会社として初となる「カーボン・ニュートラル」の認定も受けている。これは企業活動における二酸化炭素排出量について、そのすべてを計測・削減・相殺することで、企業としての総排出量実質ゼロを達成している。
さらに同年から、毎年「サステナビリティ・レポート」として、サステナビリティに関わる取り組みのすべてを公開しており、いち企業として利潤追求だけでなく、社会全体の中での企業責任を果たす姿勢をアピールしている。
また近年ではバイオ分野の研究にも注力している。アルカンターラの主な原料はポリエステルで、全体の70%を占めている。そのポリエステルの元となるポリマーは石油から作られるが、そのうち30%は既にリサイクル素材を使用しているという。ここに研究中のバイオベースポリマーが加われば、さらに製造時の環境負荷を減らすことができるだろう。
クリエイティブの分野でも存在感を示すアルカンターラ
最後はアルカンターラとクリエイティブ分野のコラボレーションだ。前述の通り、用途に合わせて様々なカスタマイズが可能なアルカンターラは、多くのアーティスト、クリエイターとも積極的なコラボレーションを行なっている。
一例を挙げると、世界的なファッションデザイナー「ヨウジヤマモト」との共同ブランド「ワイズ」の展開や、東京・六本木の森美術館で開かれた塩田千春氏の個展に素材を提供するなど、日本でもその姿を目にすることができる。
クルマにサステナビリティにクリエイティブと、幅広い活動を行なっているのがアルカンターラの特徴だ。筆者も実際に工場を訪れるまでは、恥ずかしながらひとつのマテリアルメーカーとしか思っていなかったが、今回の工場見学でその考えは180度変わった。これらのバックボーンを含めて「アルカンターラ」という価値なのだ。皆さんもこれから街中でアルカンターラを見かけるたび、イタリアのマテリアルメーカーに思いを馳せてみてはいかがだろうか?
アルカンターラができるまで
ここでは実際に工場でアルカンターラが形になり、我々の元に届けられるまでのすべての工程を見学することができたので、その模様をお届けしよう。
01.サステナブルな原料を使用
アルカンターラの原料となるポリエステルは、主に石油から作られるが、近年はリサイクル素材をベースに持つポリマー比率を高め、サステナビリティに貢献している。
02.太さ約4μmのファイバー状に
ペレット状のポリエステルは専用の金型を通して引き延ばされ、1本あたり太さ約4μmの糸として加工される。ちなみに4μmは髪の毛よりも細い。
03.洗浄と引き延ばし
04.ウェーブを加える裁断
05.圧縮機でブロック状に
06.攪拌してシート状に
07.15層のレイヤーに
08.針を上下から打ち込んで密着
09.検品の上、ロール状に
カスタマーの声に応えるアルカンターラのテイラーメイド「コンプレックス・マニュファクチュアリング」
アルカンターラの名を高級素材として一気に押し上げたのが、テイラーメイドシステム「コンプレックス・マニュファクチュアリング」だ。カスタマーのニーズに細かく応えるこのシステムの神髄に迫る。
好みのカラーに生地を染色
複雑な加工をワンストップで
レーザーパンチング/レーザーを用いてアルカンターラの表面に穴あけ(パンチング)加工を施す。シンプルな丸い穴から複雑な造形まで、この後の工程も含めてワンストップで行なわれるため、カスタマーの複雑な要望に応えることができる。
最後は人の目で検品
コンプレックス・マニュファクチュアリングで作られたプロダクト
オートモビル
アルカンターラが最も多く用いられているのは自動車の内装だ。地元イタリアのメーカーはもちろん、日本を含めて数多くのメーカーがアルカンターラを採用している。
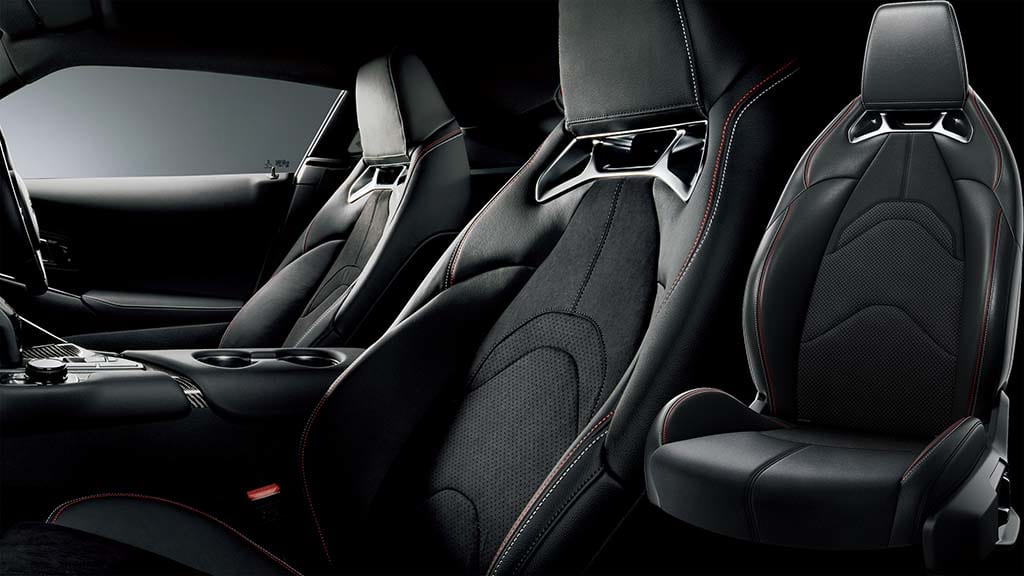
トヨタGRスープラPlasma Orange 100 Edition/トヨタGRスープラの限定車にもアルカンターラが用いられる。耐久性が高く、肌触りもよく高級感に溢れるアルカンターラは自動車の内装に最適なマテリアルだ。
コンシューマー・エレクトロニクス
ファッション
クリエイティブ
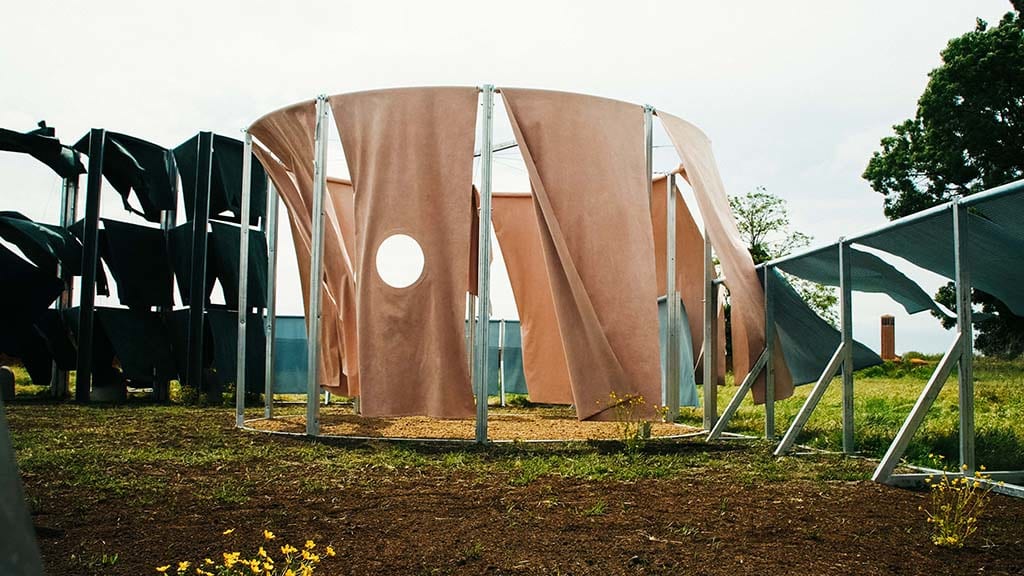
アルカンターラがとりわけ力を入れているのがクリエイティブの分野だ。世界中のクリエイターや美術館などとコラボして、アルカンターラを用いた展示や作品を発表している。複雑な加工や仕上げをワンストップで行なえるアルカンターラは、クリエイターの要望にも細かに応えることができるのだ。
アルカンターラS.p.A 代表・アンドレア・ボラーニョ氏