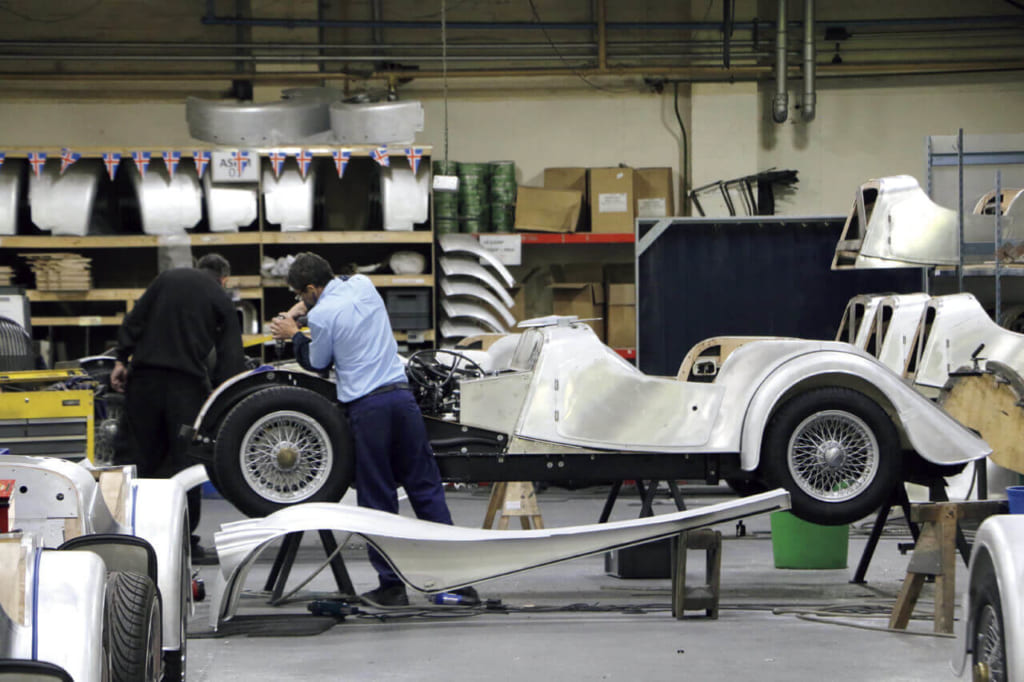
モーガンカーズ ジャパンの発足で、日本でもより身近な存在となりつつあるモーガン。いまだに車体の一部に“木”を使っているという製作現場はどうなっているのか?トップモデルであるプラス8の50周年に沸くマルヴァーンの本社工場を訪ねた。
Column 01
歴史と温もりが感じられるクラフトマンシップの宝庫
“モーガン”と聞いて、あなたは何を思い浮かべるだろうか? 100年以上にわたり、スポーツカーだけを作り続けてきた孤高のメーカー。木をボディフレームに使用する特異な構造。80年以上変わらないクラシカルな姿……。
そのイメージはどれも正しい。しかし、実際にモーガンがどうやって作られているのか知っているという方は、少ないかもしれない。
モーガン・モーター・カンパニーの本社工場は、ロンドンからクルマで3時間ほど走ったウスターシャーにある小さな街、マルヴァーン(発音的にはモルヴァーンが近い)のピッカーズレイ・ロードという通り沿いにある。
1909年にプジョー製Vツインを積んだスリーホイーラーを製作したヘンリー・フレドリック・スタンリー・モーガンが、この地に工場を構えたのは1914年夏のこと。以来、この場所でモーガンは作り続けられている。
敷地内にはいかにも古めかしいレンガ造りの建物が並列して並んでいるが、そのうちの2棟は1914年に建てられたもの。それに並ぶ2棟も1919年に建てられたものだ。
そのうちの3棟が4輪の車体製造部門となっているのだが、左の建物で外注のラダーフレーム(V8モデルはアルミモノコック)とパワートレインをドッキング。右の建物でボディのベースとなるウッドフレームを加工、製作し、中央の建物でアルミ製のアウタースキンとともにシャシー、ボディを合体させる流れになっている。
その中で目を引いたのが、モーガンのアイデンティティといえるウッドフレームの製作風景だ。
一般的に装飾部品として木を使うことは珍しくないが、今でもボディの主要構造材に木を使っているメーカーはモーガンだけだ。なぜ頑なにその伝統を守るのか?という問いに対し、マネージング・ディレクターのスティーブ・モリスは「木は加工しやすく、クラッシュにも強い、軽くて頑丈な素材。我々しか使っていないというのも大事なポイントですね」と答える。
確かに木と聞くと古臭く脆いイメージを持たれるかもしれないが、モリスの言うとおり、繊維の向きを直交させて圧着したベニア合板は、カーボンファイバーより遥か昔に生まれた軽くて頑丈なコンポジット素材なのである。
現在モーガンで使用されているのは100%英国産のアッシュ材(トネリコの一種)だ。その加工風景は、まさに家具工場か製材所といった雰囲気で、電動ノコギリで切られた部材を年季の入ったノミやカンナで成形し、ひとつずつ調整しながらネジ止めして、フレームが組み立てられていく。
一方、リアフェンダーアーチは、細長く切ったベニア合板を3枚重ねて接着し、アーチの形になった雌型で2時間挟んで(冬場はもう少し長くなる)製作するという昔ながらの工法で作られている。
そうした手間暇は、シャシー組み立て、アッセンブリー、塗装、内装組み付けなど全ての工程で同じ。また、その伝統を守るためにモーガンでは積極的に若い工員を受け入れ、自身の手で職人を育て、技術を後世へと残す取り組みも行なっている。
そんな話を聞きながら訪れた最終検査工程で1台のエアロGTが目に止まった。よく見るとボンネットフードの裏側が、ギッシリとサインで埋め尽くされている。実はこれは、「このクルマに関わった全ての職人のサインを入れて欲しい」というオーナーの意向で入れられたものだという。
世の中には高性能で、高級なハンドメイドカーは山ほど存在する。しかしながら、モーガン以上に現場の人々の温もりが込められているクルマを他には知らない。このエアロGTのオーナーもきっと同じ想いを抱いていたに違いない。

各部門で出来上がったシャシーとボディフレームにアルミ製のボディパネルを組み付け、ようやく自動車の形になる。パネルのフィッティングはハンマーを持った職人が、ウッドフレームに叩いて合わせる昔ながらの方法。
Column 02
カントリーロードで最新ラインナップに乗る!
工場見学に合わせ、現在日本に導入されている4車種−4/4、プラス4、ロードスター、3ホイーラーに試乗することができた。このうちクラシックレンジと呼ばれる4輪モデルは、最もバランスに優れすべてが手の内にある1.6リッター 直4(112ps)の4/4、パワフルながらジャジャ馬感が強く、昔のプラス8に近い味わいをもつ2.0リッター直4(156ps)のプラス4、そして唯一のパワステ装着車でパワフルながらどこかGT的な余裕が感じられる3.7リッター V6(284ps)のロードスターと、見事にキャラクターが分かれていた。一方、初体験となった3ホイーラーは、すべてがダイレクトでファン。まるでバイクでハングオンするようなコーナリングフィールは病みつきになる!
時代の変化に合わせながら、モーガンの伝統を守り続けます
世界では珍しく、一貫して創業一族が経営を続けてきたモーガンだが、2013年からスティーブ・モリスがマネージング・ディレクターとして(オーナーはモーガン家)陣頭指揮を採っている。ちなみに彼は16歳の時に職工として入社して以来、35年以上にわたって一筋で勤め上げてきたという生粋の“モーガン・マン”(愛車はエアロGT)である。「EV3の販売がもうすぐ始まりますし、ハイブリッドや水素燃料電池車など未来のテクノロジーの開発も進めています。伝統に縛られて立ち止まるのではなく、時代に合わせてモーガンも変わっていきます。でもモーガンのDNAが失われることはありません。状況が許す限りクラシックなモデルも作り続けます」。