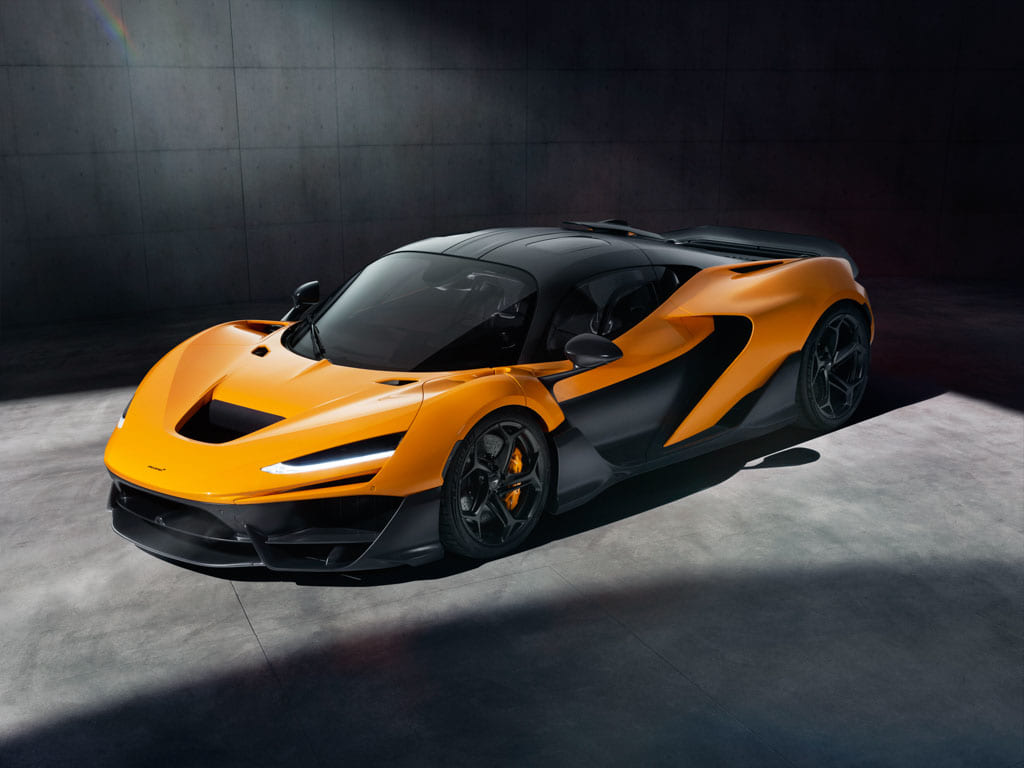
マクラーレンの軽量エンジニアリングにおける世界トップクラスの専門知識が培った、カーボンファイバー製シャシー技術
マクラーレンは、60年以上にわたってF1で開発された革新的なテクノロジーのリーダーとして、軽量スーパーカーエンジニアリングのスタンダードを確立する画期的な自動車テクノロジーを提供する上で有利な立場にある。
そして、マクラーレンの革新的な能力を強く表しているのがカーボンファイバーである。軽量、高強度、高剛性を誇るマクラーレンは、材料科学の高度な技術分野における世界的リーダーとして半世紀を迎えようとしており、可能性の限界を押し広げ続けている。
カーボンファイバーは、公道でもサーキットでも最高の特性を併せ持つスーパーカーを提供するために不可欠な役割を果たしている。初代「マクラーレンF1」以来、マクラーレンの市販車はすべて、この複合材料で作られたシャシーをベースにしている。
この素材の軽量性と剛性は、ベンチマークとなるパフォーマンスとスリリングなダイナミクスを実現するだけでなく、クラスをリードする乗り心地と、効率性という付加的なメリットをもたらす鍵となる。その強度は、安全性、保証、耐久性を提供する。
この素材は、スーパーカーのプラットフォームを構築するのに最適な素材であり、驚異的なパッケージング・ソリューションによって、デザイナーは驚異的な美観と空力効率を備えたクルマを創り出すことができる。
【写真18枚】いまや”F1のスタンダード”。カーボンファイバー製モノコック
マクラーレンのF1の伝統にしっかりと根ざしたテクノロジーを載せた名車たち
MP4/1(1981年)
「MP4/1」は、フルカーボンファイバー製モノコックシャシーを採用した初のレーシングカーとして、F1に革命をもたらした。その軽量かつ高剛性の構造は、安全性とパフォーマンスを大幅に向上させた。ジョン・バーナードが設計したこの先駆的なシャシーは、モータースポーツにおけるカーボンファイバーの普及につながり、F1マシンのデザインを一変させた。
F1にカーボンファイバーシャシーが導入されたことで、F1は近代化された時代を迎えた。安全性の面でもカーボンファイバーの優位性は、1981年のイタリアGPで見事に証明された。マクラーレンのドライバー、ジョン・ワトソンは、時速140マイル(時速約140km)で発生した大事故から無傷で生還。
この事故は、カーボンファイバー製シャシー・テクノロジーがF1における安全性の未来形であることを、広くF1パドックに確信させる大きなきっかけとなった。そのわずか3レース後、ワトソンがその年のイギリスGPで40秒以上の大差をつけて優勝を飾ったことで、カーボンシャシーのパフォーマンスのポテンシャルが明らかになった。
マクラーレンF1(1993年)
マクラーレンF1の画期的なデザインは数多くあるが、なかでもカーボンファイバー製モノコックシャシーとフルカーボンファイバー製ボディの採用は、最小限の重量と最大限の構造剛性を重視したものである。ロードカーにおけるカーボンファイバー使用の先駆者であるF1は、わずか1,140kgという軽量さと、6.1L V12エンジンから627PSという絶大なパワーを得て、比類ないパフォーマンスを誇った。
カーボンファイバー製モノコックは、当時最先端のコンピューター支援設計と解析を駆使して設計され、F1はロードカーでは前代未聞の大幅なパワーウェイトレシオを達成し、スーパーカーエンジニアリングの象徴となった。また、F1 GTRが1995年のル・マン24時間耐久レースで優勝したことで、カーボンファイバー技術がサーキットから公道へ、そしてまた公道へと完全に循環することになった。
マクラーレン12C(2011年)
マクラーレン・オートモーティブが最先端のマクラーレン・プロダクション・センターで生産した初のロードカーである「マクラーレン12C」は、モノセルを導入した。モノセルとは、シングルピースのカーボンファイバー製チューブのことで、当時のロードカーとしては前例のない剛性と軽さを実現した。
このシャシーの開発により、マクラーレンのカーボンファイバーは21世紀を迎えた。モノコックシャシー「モノセル」は、世界初の真に大量生産されたフルカーボンファイバー・タブのスーパーカー・シリーズのバックボーンであり、この種のシャシー構造の利点を、これまでの自動車業界では見られなかった規模で実現した。
モノセルは、12Cがスーパーカーセグメントに導入した画期的な新技術のひとつであると同時に、マクラーレンの現代的なスーパーカーのDNAを築き上げ、未来への礎を築いた中核的要素のひとつでもある。
当時まだ一般的であったアルミニウム・デザインに対する12Cの優位性は、チューブ自体の重量がわずか75kgという驚異的な軽さだけでなく、12Cのスパイダー・ヴァリアントがシャシーの追加補強を必要としないほどの優れたねじれ剛性にあった。
マクラーレンP1(2013年)
12Cの発表からわずか2年後、マクラーレンは2013年に「マクラーレンP1」を発表し、再びカーボンファイバー製スーパーカーのテクノロジーに革命を起こす。
マクラーレンの”1″ カー・ラインナップの第2弾となるこのモデルは、ルーフとロア構造、ルーフ・シュノーケル、エンジン・エアインテーク・キャビティだけでなく、P1の高性能ハイブリッド・パワートレインに不可欠なバッテリーとパワーエレクトロニクスのハウジングをモノケージと呼ばれる構造に組み込んだフルカーボンファイバー製ボディ構造を採用することで、その前身であるマクラーレンF1からさらに一歩前進した。
この構造全体の重量はわずか90kg。スーパーカーのエンジニアリングとパッケージングにおける傑作であり、電動化は車両全体の重量を妥協する必要はなく、真の軽量アルティメット・スーパーカーとしてパフォーマンスを発揮する上で不可欠な役割を果たすことができることを世界に証明した。
マクラーレン720S(2017年)
「720S」では、現在も「マクラーレン750S」に採用されているモノケージIIカーボンファイバー構造が導入され、前身のモノセルに比べて剛性のさらなる向上と軽量化が図られた。
この軽量構造はパッセンジャー・セル全体を構成するもので、カーボンファイバー製チューブとカーボンファイバー製アッパー・ストラクチャーを組み合わせることで、軽量性をさらに高めている。量産スーパーカーにおけるカーボンモノコック技術の大きな前進は、数々の賞を受賞したパフォーマンスとダイナミクスだけでなく、人間工学、視界、デザインも大幅に改善した。
モノケージIIの驚くほどスリムなルーフピラーは、ウィンドスクリーンを通して抜群の視界をもたらし、キャブフォワードのコックピットの後方に配置されたBピラーと相まって、モノケージIIは格別な空間感覚に貢献している。
モノケージIIのシルは乗員の足元に向かって下がり、乗降性を高めている。ドラマチックなダブルスキンのディヘドラルドアは、開くと前方から上方に向かってヒンジが開き、その過程でルーフの一部が取られる。カーボンセルは、乗り降りのしやすさと同様に、最大限のパフォーマンスを引き出すスーパーカーを実現した。
モノセルによってもたらされた利点のように、720Sと750Sのスパイダー・バージョンでは、カーボンファイバー製の特注のリア上部構造が採用され、それに伴う追加強化や補強は必要なく、スリリングなダイナミクスと最小限の重量増加を実現している。
マクラーレン・コンポジット・テクノロジー・センターの開設(2018年)
2018年、英国シェフィールドに「マクラーレン・コンポジット・テクノロジー・センター (MCTC)」がオープンし、ウォーキング郊外初の独立したマクラーレンの生産施設に5,000万ポンド(約95億2700万円)が投資された。
マクラーレン・オートモーティブ、シェフィールド大学のAMRC、シェフィールド市議会のパートナーシップによって設立されたこの世界クラスの施設は、複合材料のエンジニアリングと研究だけでなく、将来のパワートレイン技術と直接統合できる新世代のカーボンファイバー製チューブの生産においても卓越したセンターとなることを目指している。
MCTCで製造される最初のカーボンファイバー製量産部品は、驚異的な超軽量を誇る「マクラーレン765LT」のためのもので、同車のアクティブ・リアウィング、リアバンパー、フロントフロアはMCTCで設計、デザイン、製造される。
マクラーレン・アルトゥーラ(2021年)
「マクラーレン・アルトゥーラ」は、新世代の高性能ハイブリッド・パワートレインを統合するために特別に設計されたマクラーレン・カーボン・ライトウェイト・アーキテクチャー(MCLA)を導入。
従来のシャシーよりも軽量かつ高強度なMCLAは、アルトゥーラのハイブリッドV6パワートレインをサポートすると同時に、カーボンファイバー製モノコックを使用することによる構造上の利点をさらに最適化し、発展させ続けている。MCLAは、マクラーレンにとって初めてウォーキング本社以外の主要施設で製造されており、シェフィールドにあるマクラーレン・コンポジット・テクノロジー・センターで生産される。
MCLAは、カーボンファイバー製モノコック技術における革命的な瞬間であり、これまでモノセルおよびモノケージII構造で開発されてきた軽量性と剛性の利点が強化されただけでなく、アルトゥーラで使用されるハイブリッドシステムのバッテリー用セーフティセルが組み込まれ、さらに衝突や荷重に耐える機能がタブに統合されている。
マクラーレンの革新的なテクノロジーにより、アルトゥーラのMCLAカーボンファイバー製モノコックは、これまでにない大量生産が可能になりました。そして「アルトゥーラ スパイダー」の発表により、マクラーレンは軽量スパイダーのDNAを継承し、「アルトゥーラ スパイダー」のシャシーにはクーペモデル以上の強化や補強は必要ない。
マクラーレンW1(2024年)
マクラーレンW1は、マクラーレンの軽量カーボンファイバーDNAの進化を継続し、ロードカー用に設計された中で最も先鋭的で技術的に先進的なカーボンファイバー製チューブであるエアロセルが登場する。
プリプレグカーボンファイバーを使用したこのテクノロジーは、ハイパー専用モデルであるサーキット専用モデル「ソルスGT」にも採用されているもので、硬化プロセスを簡素化する樹脂システムをあらかじめ含浸させたコンポジット材を使用する。その後、金型内で圧力処理が施され、エアロセルは同等のチューブよりも高い構造強度を持つ。
その結果、W1のデザインで追求された軽量化のメリットである、車体外装のところどころに追加ボディワークを必要としない、より軽量なチューブが実現した。エアロセルはまた、W1の究極の空力パッケージの重要な要素として設計され、真のグランドエフェクトを利用している。
モノコックのフロアを65mm高くすることで、フットウェルの位置が上がり、エアロセルの前方に向かって80mmまで上昇している。同時に、エアロセル、そして車両全体の長さを短くするために、シート位置を固定し、モノコックに座席を組み込むという決断が下された。ホイールベースを約70mm短縮することで、さらなる軽量化も実現した。
マクラーレンW1には、マクラーレンの次世代カーボンファイバー技術であるマクラーレンARTカーボンファイバーも導入されている。マクラーレンの画期的な「ART (Automated Rapid Tape) “高速”成膜製造技術」の開発により実現したマクラーレンARTカーボンファイバーは、エンジニアの新たな可能性を引き出す。マクラーレンW1のアクティブ・フロント・ウイングは、この新技術のデビューとなる。
「カーボンファイバーは、マクラーレンを語る上で欠かせないものであり、私たちのDNAの中核をなすものです。カーボンファイバーは、マクラーレンを語る上で欠かすことのできないものであり、私たちのDNAの中核をなすものです。
カーボンファイバーによって、最高のダイナミック特性を備えた超軽量スーパーカーを実現することができるのです」と、マクラーレン・オートモーティブ最高経営責任者のマイケル・ライターズCEOだ。